EDM (Electrical discharge machining), also known as spark machining or spark eroding, is a manufacturing process of creating a desired part from the metal sheet by using electrical discharges (sparks). There are three types of EDM: Sinker EDM, Wire EDM, and Fast hole drilling EDM. Wire EDM, also known as wire electrical discharge machining (WEDM) or wire-cut EDM, involves using a thin single-strand metal conductive wire, like brass, along with de-ionized water allows the wire to cut through metal with the heat from electrical sparks.
Understanding The EDM Process
During the EDM process, a metal part is placed into dielectric fluid, and a wire is fed through the submerged metal component. An electric current is sent through the part to create the sparks that will ultimately help form the desired shape of the component.
When the distance separating the electrodes narrows, it increases the intensity of the electric field, and thus increases the strength of the dielectric fluid. The current more easily passes between the two electrodes under these conditions, leading to the separation of the component from the metal sheet with each spark.
After the currents have passed through and the desired shape has been achieved, manufacturers will sometimes perform a process called “flushing,” using a dielectric liquid to help remove any leftover material or waste from the finished product.
Benefits And Applications Of Wire EDM
The wire EDM machine, also known as a “cheese cutter,” offers several unique advantages, making it a popular choice for manufacturers across a range of different industries.
EDM Benefits
Wire EDM machines are able to carefully remove excess material without exerting a strong cutting force. The process is often automated, meaning it has less chance of causing damage to the workpiece itself. And because wire EDM machines can accommodate hard materials, there is no need for secondary, post-machining thermal treatments. As a result, there is little to no heat stress placed on the shaped part, and less chance that the surface of the part will become distorted.
EDM Applications
Wire EDM is most commonly used in mold and die manufacturing processes, particularly for extrusion dies and blanking punches. EDM can be used in everything from prototypes to full production runs, and is most often used to manufacture metal components and tools. The process is best suited for applications requiring low levels of residual stress.
EDM Industries
EDM is most commonly used to manufacture parts and components for the automotive, aerospace, and electronics industries.
Tips For Wire EDM
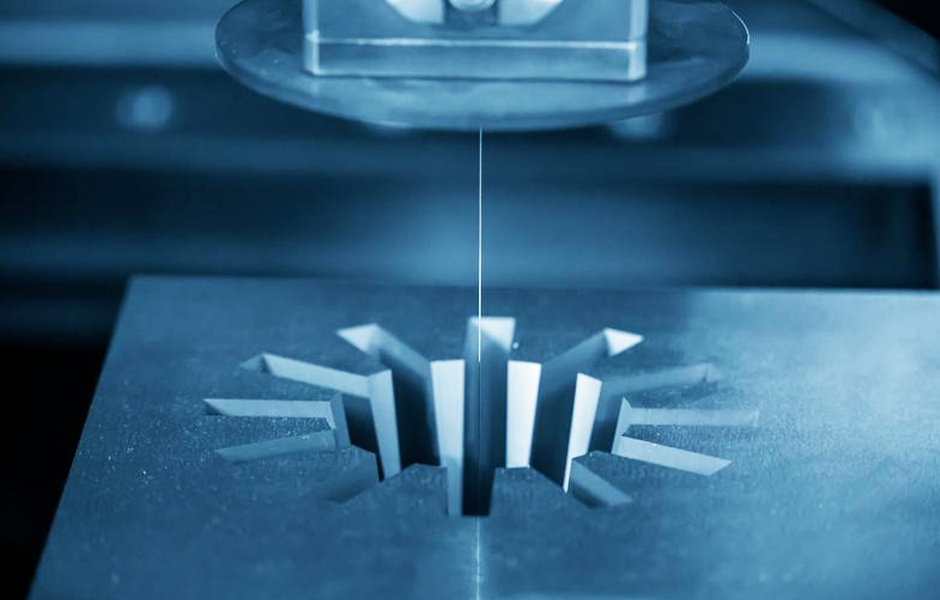
WEDM programming is the focus of the entire process. The machine tool is processed according to the numerical control program. The correctness of the program directly affects the processing shape and processing accuracy. Most of the actual production uses automatic programming methods.
After the programming is completed and before the formal cutting process, the CNC program should be checked and verified to determine its correctness. The numerical control system of the wire EDM machine tool provides a method of program verification. The commonly used methods are: one is the drawing inspection method, which is mainly used to verify whether there is an error syntax in the program and whether it conforms to the pattern processing contour. The other is the empty stroke inspection method , it can check the actual processing of the program, check whether there is collision or interference in the processing, and whether the stroke of the machine tool meets the processing requirements, etc., through the simulation of the dynamic processing situation, the program and the processing path are fully verified.
For some punching dies with high dimensional accuracy requirements and small matching gaps between convex and concave dies, you can first try cutting with a thin sheet to check the dimensional accuracy and matching gaps. If you find that it does not meet the requirements, you should revise the program in time until the verification is qualified. During processing, electrical and non-electrical parameters can be adjusted according to the processing state to keep the processing in the best discharge state. After the formal cutting is over, do not rush to remove the workpiece, check whether the start and end coordinate points are consistent. If any problems are found, “remedial” measures should be taken in time.
Rapid CNC Machinign Service
At Dfm CNC Shop, we provide high-quality prototyping, rapid tooling and low-volume manufacturing services to support your product development needs.
Our provides a variety of precision CNC machining services including milling, turning, EDM, wire EDM and surface grinding. We can handle all types of CNC machining parts in both metal and plastic materials. Contact us today for a free quote